Frequently Asked Questions
The Exar controllers, regulators and power modules are powered by an internal LDO to produce the Vcc rail that their circuits need to run properly. If the input voltage that feeds the LDO is the minimum Vin as specified on the datasheet or above, the Vcc is enough to power the device and the Vin, Vcc and PVIN pins can be connected together.
If the input voltage is 5V, then the Vin and Vcc pins can be tied together and the input voltage is fed to the PVIN pin.
If input voltage is below 5V, then a separate low current 5V supply (common in many systems) is connected to the Vin and Vcc pins which are tied together to keep the device running properly. The input voltage is connected to the PVIN pin.
Voltage mode PWM
Voltage mode PWM is a simple technique that uses a single loop to control the output voltage. As shown in Figure 1, the output voltage is compared to a reference voltage with an error amplifier. The output of the error amplifier is then compared to a sawtooth and that output is used to drive the MOSFET, usually via a voltage divider.
Figure 1
As shown in Figure 2, the output voltage is modulated by turning the high-side FET on (on-time) with the pulse width and turning the low side FET off. At the end of the pulse, the high-side FET is turned off (off-time) and the low side FET is turned on until the next pulse. Vout = On-Time/Period * Vin.
The advantages of voltage mode PWM is that it is a very simple, common, smaller solution with good accuracy. The disadvantages are that complex frequency compensation is required (two poles) to stabilize the loop and because trailing edge control is most commonly used, there is a delay in load step response.
Current mode PWM
With voltage mode PWM, current is less known. For better control, current mode PWM senses the inductor current and it is compared to the reference voltage as shown in Figure 3.
Figure 3
Although the current has to be sensed with accuracy and introduces noise, the advantages of current mode PWM are easier loop compensation (less compensation needed with one pole), and it is easier to implement over-current protection and parallel currents to the output.
Standard Constant On-Time (COT)
As opposed to PWM, the pulse width in COT is always the same as shown in Figure 4. Instead the off-time length varies (as does the frequency) which modulates the output. As the Vout increases, the off-time of the duty cycle increases (frequency decreases) and the fixed on-time produces a lower duty cycle. This transfers less energy to the output and lowers the Vout. More simply said, as Vout increases, the duty cycle decreases. Conversely, as the Vout decreases, the off-time of the duty cycle decreases (frequency increases) and the fixed on-time produces a higher duty cycle. This transfers more energy to the output and raises the Vout.
Figure 4
The advantages of standard COT are very fast transient response, simplicity (inexpensive) and that frequency compensation is not complex as it is in PWM control. However, the feedback signal tends to have low amplitude and signal to noise ratio, making it very noise sensitive. Also, the output voltage is higher than the reference voltage and the ripple is dependent on and sensitive to the output capacitor ESR. This introduces a DC offset which is the average amount the output voltage is over the reference voltage. It is also jitter prone and the frequency changes during the load steps.
Some solutions solve the noise sensitivity by having one of two options that condition the feedback signal but introduce delays. One tradeoff provides faster transient responses; the other allows low ESR output capacitors to be used.
MaxLinear’s patented COT
MaxLinear’s patented COT architecture however conditions the reference instead as shown in Figure 5. The MaxLinear devices create their own emulated ramp that is insensitive to noise and the ESR of the capacitor. Since the output capacitor ESR does not affect it, low ESR ceramic capacitors can be used and maintain stability without decreasing speed. In addition, the Vout and reference voltage are compared and that result controls the ramp circuit. This creates a slower loop where the output voltage is averaged out and the DC offset is not introduced as in standard COT.
Figure 5
MaxLinear’s COT still has the standard COT advantages of very fast transient response, simplicity and no complex frequency compensation in addition to not having DC offset or ESR value sensitivity. MaxLinear’s COT architecture provides exceptional line and load regulation.
The XR76117 and XR76121 are identical to each other except for their output current rating. Similarly the IR3824/IR3825/IR3829 are identical to each other except for the differences shown in this section. Output current ratings are summarized in Table 1.
Spec | Exar XR76117 / XR76121 | Infineon IR3824 / IR3825 / IR3829 |
Max IOUT | 15A (XR76117); 20A (XR76121) | 15A (IR3824); 16A (IR3829); 20A (IR3825) |
VIN range | 4.5V to 22V | 5V to 21V |
VOUT range | 0.6V to 18V | 0.6V to 0.86 x VIN |
Frequency range | 200kHz to 1MHz | Up to 1.5MHz |
Temperature range | -40°C to 125°C | -40°C to 125°C |
Supply current | 17mA | 20mA |
Table 1: Major Specification Comparison
Pin | XR76117 / XR76121 | IR3824 / IR3825 / IR3829 | Same Function / Connection? | Changes Required to Drop XR76117/21 into IR3824/25/29 Socket |
1 | FB | Fb | Yes/Yes | None |
2 | FCCM | NC | No/No | Must either be tied to VCC for FCCM operation or tied to GND for CCM/DCM operation. Pull-up or pull-down resistors may also be used. See Figure 2 and XR76117 or XR761121 datasheet for more information. |
3 | AGND | Comp | No/No | Add a 0Ω resistor to jumper pin 3 to pin 4 and do not stuff compensation Cs/Rs. Refer to Figure 2. |
4 | AGND | Gnd | Yes/Yes | None |
5 | TON | Rt | No/Yes | In both cases, this pin sets frequency and requires a resistor to GND. However, a different resistor value must be used for the XR solution. Refer to the XR76117 / XR76121 datasheet for resistor value calculation. |
6 | ILIM | ILIM | Yes/No | Add a 0Ω resistor to connect to SW. Do not stuff resistors to VCC or GND. Refer to Figure 2. |
7 | PGOOD | PGood | Yes/Yes | None |
8 | VSNS | Vsns | Yes/Yes | None |
9 | VIN | Vin | Yes/Yes | None |
10 | VCC | Vcc/ LDO_Out | Yes/Yes | None |
11 | PGND | PGnd | Yes/Yes | None |
12 | SW | SW | Yes/Yes | None |
13 | PVIN | PVin | Yes/Yes | None |
14 | BST | Boot | Yes/Yes | None |
15 | EN | Enable | Yes/Yes | None |
16 | SS | NC | No/No | Add an external capacitor to GND. See Figure 2 or the XR76117/XR76121 datasheet for more information. |
17 | AGND PAD | GND | Yes/Yes | None |
Table 2: Pin-out Comparison & Changes Required to Drop XR76117 / XR76121 into IR3824 / IR3825 / IR3829 Socket
The PCB board can be easily designed to drop-in the XR76117 or XR76121 while maintaining compatibility to the IR3824/25/29. In Figure 2 below, pinning for both series are represented. The Exar XR76117 and XR76121 pin names do not have parenthesis, and the same corresponding pins for the IR3824/25/29 are in parenthesis. As shown in the legend, the components in green boxes are added and the ones in red boxes are omitted when using the XR76117 or XR76121. Both a pull-up and pull-down are shown for pins 2 and 6, but only one or the other will be present depending on the application. So, 4 passives (red) will not be populated while 3 passives and a jumper will be populated.

With a plethora of equipment with built in USB ports, USB hubs assist by expanding the number of USB ports available to plug devices into in a network. In its simplest form, a USB hub is plugged into a host computer’s USB interface. A hub has one upstream path (going back towards the host’s USB interface) and multiple downstream paths (going towards the end devices). Another downstream hub could be plugged and cascaded into the first hub and so on up to 7 tiers and 127 ports. There are limitations on USB cable length, however a USB hub can function as a repeater if more length is needed. See AN213 section 3.0 for more information.
USB is governed by industry specification http://www.usb.org/developers/docs/usb20_docs/ .
MaxLinear XR22404 and XR22414 USB hubs have 4 available downstream ports while the XR22417 provides 7. All 3 parts have a USB 2.0 compliant interface, meaning that the upstream is capable of high speed (480Mbps) and may operate at high (480Mbps) or full speed (12Mbps). Downstream can operate and high (480Mbps), full (12Mbps) or low speed (1.5Mbps).
USB 2.0 host ports provide up to 5 unit loads of 100 mA per attached peripheral device (including USB hubs). A bus powered hub, powered from USB host 5 volt VBUS, can supply a maximum of 1 unit load on each of its downstream ports. For example, a 4-port hub must be able to supply 4 x 100 mA or 400 mA total and is also allotted 100 mA for its own power requirements. A hub with more than 4 downstream ports cannot be bus powered.
Conversely, a self-powered hub is powered by an outside power source. It is restricted in the number of downstream ports and the power to those ports only by the power from the external source. A self-powered hub should typically be able to provide a minimum of 5 unit loads per downstream port.
MaxLinear has a number of USB 2.0 hub products. The 4-port XR22404, XR22414 and 7-port XR22417 all support self-powered mode while XR22404 and XR22414 can also be bus-powered. The XR22404 can provide battery charging on its downstream ports, but must be in self-powered mode to do so.
STT (Single Transaction Translator) is where one TT splits transactions and polls round robin to translate to multiple downstream peripheral devices, such as in the case of the XR22404 that shares the bandwidth. MTT (Multiple Transaction Translator) is where several are provided. The XR22414 provides one for each of the 4 downstream ports, while the XR22417 provides one for each of the 7 downstream ports. A dedicated TT for the downstream ports provides each the highest bandwidth capability, 12Mbps each in the case of full speed.


Either an individual or ganged power mode can be employed. In ganged mode all ganged ports are monitored by one power monitoring device and global current sensing is used. However in an over-current condition, all ganged ports are disabled. In individual mode each downstream port monitors over-current and can disable power independently. XR22404 uses ganged power mode and global overcurrent sensing. XR22414 can be configured for either ganged or individual power mode as shown in its datasheet. XR22417 uses individual power mode.
The hub then signals the USB host and the host marks the port. SP2525A or SP2526A can be used in conjunction with the XR22404, XR22414 and XR22417 devices.
For some UARTs, Microsoft certified drivers are available for Windows Operating System and can be downloaded via Windows Update. These drivers and others, including for Linux and other Operating Systems can be found by visiting https://www.exar.com/design-tools/software-drivers Please note Software Driver Use Terms.
Click on the version link under Driver Version of the desired type of UART, part number and operating system. A zip file is downloaded which contains a ReadMe file with instructions.
Links to datasheets and product family pages are in the software driver table for easy reference.For RS-232 it is 50 feet (15 meters), or the cable length equal to a capacitance of 2500 pF, at a maximum transmission rate of 19.2kbps. When we reduce the baud rate, it allows for longer cable length. For Example:
Baud Rate (bps) | Maximum RS-232 Cable Length (ft) |
19200 | 50 |
9600 | 500 |
4800 | 1000 |
2400 | 3000 |
Fail Safe is an attempt to keep the output of the RS-485 receiver to a known state. Transceivers may have standard fail safe or advanced / enhanced receiver fail safe features. Standard fail safe supports open inputs while enhanced fail safe transceivers such as the SP339 and XR34350 support open input, shorted input and undriven terminated lines without external biasing. See Application Note ANI-22 for more detail.
The XR17Cxxx, XR17Dxxx, and XR17Vxxx are all UARTs but have the following basic differences:
- PCI UARTs
- XR17Cxxx – 5V supply, up to 33MHz clock input
- XR17Dxxx – 5V or 3.3V supply, up to 33MHz clock input
- XR17V2xx – 3.3V supply, up to 66MHz clock input
- PCIe UARTs
- XR17V3xx – 3.3V supply, up to 125MHz clock input
Find the product page of the part that you want to get an evaluation board for and click on Parts & Purchasing. Example:
Click on Parts & Purchasing or Order Now. Locate the icons under Buy Now or Order Samples:
Click on the Buy Now icon and see who has stock and click on the Buy button:
Alternatively, you can click on the Order Samples icon to request a sample.
Note, not all products are sampleable from the website.
If the icons are missing, create a support ticket.
Yes, this is possible using one RS-485 transceiver. The microcontrollers will have to be addressable and have tri-state outputs. The RS-485 device can be controlled by the host via the DE/RE pin. The micros will have to be in either receiving mode or tri-state mode when the RS-485 transceiver is transmitting data. When the host transmits it will have to send an address to the specific micro. If any micro transmits the transceiver will have to be in receiving mode and all other micros will have to be in receive or tri-state. So the host would have to initiate this sequence by addressing the micro first then switch the transceiver to receive.
The half duplex system would have a bus with one transceiver and multiple microcontrollers all tied to the bus. For 5V systems the SP485 family can be used. For 3V systems the SP3070 family can be used. The require speed will determine the part number. The SP3078 part runs up to speeds of 16Mbps. See the parametric search on https://www.exar.com/products/interface/serial-transceivers/rs485-422 for more options.
Care must be taken to assure the transceiver can drive the multiple micros in RX mode.
ESD tests are “destructive tests.” The part is tested until it suffers damage. Therefore parts cannot be 100% tested in production, instead a sample of parts are characterized during the product qualification. The test procedure consists of “zapping” pins with a given voltage using the appropriate model and then running the part through electrical tests to check for functionality or performance degradation.
ESD is caused by static electricity. In order for an ESD event to occur there must be a buildup of static charge. Very high charge levels are actually quite rare. In a normal factory environment, taking basic ESD precautions (grounding-straps, anti-static smocks, ionizers, humidity control, etc.) static levels can be kept below a few tens of volts. In an uncontrolled environment, like an office, static levels rarely get above 2000 volts. Under some worstcase conditions (wearing synthetic fabrics, rubbing against synthetic upholstered furniture, extremely low humidity)
levels can go as high as 12 to 15 thousand volts. Actually to get to 15000 volts or higher you would need to be in an uncomfortably dry environment (humidity below 10%) otherwise static charge will naturally dissipate through corona discharge. It would definitely be considered a “bad hair day.” Humans can generally feel a static shock only above 3000 volts. A discharge greater than 4000 volts can cause an audible “pop.” But repeated lower level discharges can be imperceptible and still may have a cumulative damaging effect on sensitive ICs. All ICs, even those with robust protection, can be damaged if they are hit hard enough or often enough.
Most ICs in a typical system are at greatest risk of ESD damage in the factory when the PCB is assembled and the system is being built. After the system is put together they are soldered onto the PCB and shielded within a metal or plastic system enclosure. Interface ICs are designed to attach to an external connector that could be exposed to ESD when a cable is plugged in or when a person or object touches the connector. These interface pins are most likely to see ESD exposure and therefore benefit from additional protection.
Actually the letter “E” could have two different meanings, depending on where it is in the part number. Most of our interface devices are available in different temperature grades. Commercial temperature (0 to 70C) has a “C” after the numeric part number. Industrial-extended temperature (-40 to +85C) use the letter E. So for example SP485CN is commercial and SP485EN is industrial. The second letter indicates the package type, in this case N for narrow-SOIC. Another E in the suffix indicates that this device has enhanced ESD protection, typically of ±15000Volts on the interface pins. Devices that do not have the enhanced ESD still contain built-in ESD protection of at least ±2000Volts. For example the SP485ECN is ESD rated up to ±15kV, and the SP485CN is rated for ±2kV HBM.
In PWM controllers, frequency is constant and tON (on-time) is set by the controller to regulate the output voltage. However in COT controllers, the tON is constant and set by the RON resistor. This also sets the frequency. RON is connected between the TON pin and GND.
If the high-side FET was ideal, the tON of the SW signal would be equal to tON of GH (high-side FET gate) signal and the relationship between RON and tON would be:

However, the high side FET has rise and fall times as well as on and off delay times, so the tON of SW is not equal to GH. This non-ideal characteristic is measured for each regulator or module where the above equation is modified. In the Applications Information of each regulator or module datasheet, an equation defining the relationship of RON and tON is given based on test data for that device. For example, in the XR79206 power module datasheet, you will find the following equation in the Programming the On-Time section of the Applications Information:

The correlation of this equation to the test data is also given in the datasheet. In the XR79206 example, Figure 5 in the Typical Performance Characteristics section shows very good correlation:


However, as no Buck Converter is ideal, test data is taken to determine a more accurate equation which is also given in the datasheet. In the XR79206 example, the following equation is given based on test data:

Substituting this tON equation into the above equation relating RON and tON and simplifying, we get:

Then RON can be easily chosen based on the targeted VIN, VOUT, frequency and efficiency. So for example in the XR79206, if VIN = 24V, VOUT = 5V, f = 500kHz and efficiency = 90%,


As IOUT increases, frequency increases slightly due to increasing power losses. As losses increase, more power must be delivered per cycle to keep VOUT constant. Because tON is constant, the period decreases and frequency increases, as can be seen in the following example from the XR79206 datasheet:
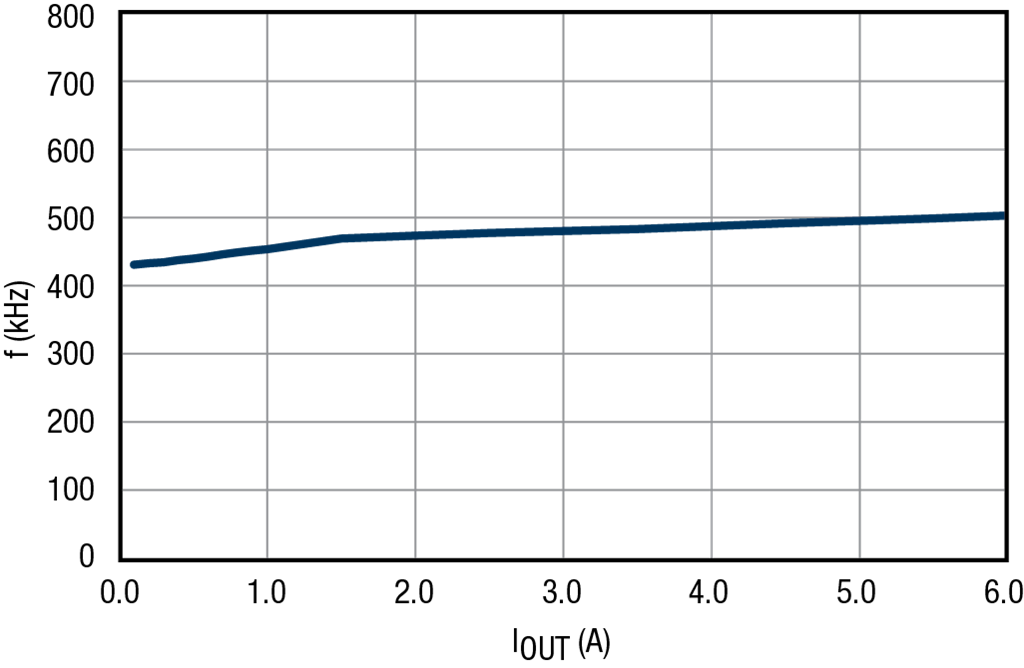
https://www.exar.com/quality-assurance-and-reliability/lead-free-program
No, the maximum fault tolerance of the above devices is ±18V only. However, the XR3305x and XR3315x families DO support up to ±60V fault tolerance. To find the device in the XR3305x and XR3315x families with the configuration you are looking for, use the parametric search https://www.exar.com/products/interface/serial-transceivers/rs485-422. The Fault Tolerance column is on the right side of the table. See the filters on the left for device selection. See Application Note ANI-23 https://www.exar.com/ani-23.pdf for more on fault testing of these devices.
For any voltage above ±60V, refer to diode manufacturers, such as the Bourns RS-485 transient protection for example below, for an external diode to absorb the transient or surge voltage for protection.
https://www.digikey.com/product-detail/en/bourns-inc/RS-485EVALBOARD1/RS-485EVALBOARD1-ND/2658335
orhttps://www.digikey.com/product-detail/en/bourns-inc/RS-485EVALBOARD2/RS-485EVALBOARD2-ND/2658336
Visit the product page for the part you are interested in. The part's status is listed in the Parts & Purchasing section. You can also view Product Lifecycle and Obsolescence Information including PDNs (Product Discontinuation Notifications).
To visit a product page, type the part into the search window on the top of the MaxLinear website.
In this example, we searched for XR33180. Visit the product page by clicking the part number or visit the orderable parts list by clicking "Orderable Parts".
The Parts & Purchasing section of the product page shows the Status of all orderable part numbers for that product. Click Show obsolete parts, to see all EOL or OBS products.
The instructions for adding the Multi-function Driver are described by Microsoft:
https://msdn.microsoft.com/en-US/library/ff794057(v=winembedded.60).aspx
When using the native CDC-ACM driver the USB UARTs defaults to HW RTS/CTS flow control. Please see the datasheet:
https://www.exar.com/product/interface/uarts/usb-uarts/xr21b1422
section on CDC-ACM driver and Table 2.
You can test to see if there is data by grounding the CTS input.
USB peripheral devices may operate in bus or self-powered modes. In bus powered mode, the peripheral device is powered by the USB host 5V VBUS power either directly, or for example through a voltage regulator that might provide a regulated 3.3V to the device from the 5V VBUS input. In self-powered mode, power to the peripheral device comes from another source other than the USB host VBUS. For example, power might come from an AC to DC converter.
MaxLinear USB to serial / UART(s), USB hubs and USB to Ethernet devices all comply fully to USB standards and are fully USB compliance tested. One USB compliance test ensures that self-powered peripheral devices do not have “back voltage” when disconnected from the USB host, on either the USB data signals (USBD+ / USBD-) or the VBUS power itself.
All MaxLinear USB UARTs, hubs and USB to Ethernet devices are USB full speed or high-speed devices. As such, they have an internal pull-up on the USBD+ signal to “advertise” their speed rating. The VBUS_SENSE pin on these devices must be connected to VBUS from the host, or upstream device if that is not the host, such that the device “senses” the disconnection from the host or upstream device. The default power mode advertised to the USB host for all USB UARTs and USB to Ethernet devices is bus powered mode. Self-powered mode can be programmed in either the internal OTP memory or external EEPROM for self-powered mode. For MaxLinear hubs, an external pin controls the power mode advertised to the USB host, except the XR22417 which must always be operated in self-powered USB mode.
1. Native drivers: Native drivers may be found in all major OS such as Windows, Linux, and Max OSX. Typically these drivers will be automatically loaded. In some cases, these are basic drivers and may have limitations on advanced device functionality, however. USB HID, Hub and CDC-ACM drivers are examples of native drivers. The CDC-ACM driver be used with our CDC-ACM class USB UARTs, but has limited functionality.
2. MaxLinear custom drivers: MaxLinear custom drivers may be used to support additional functionality in MaxLinear devices. For example, the MaxLinear custom driver for USB UARTs overcomes the limitations of the native CDC-ACM driver. See https://www.exar.com/design-tools/software-drivers for a list of and access to the drivers that we currently have. In some cases, the MaxLinear driver can also be customized, or source code can be provided after executing a Software License Agreement.
Yes: Go to the product page (XR22804 example below), click on the documentation tab on left, click on “Sample USB UART GUI” under Software:

The SP485E offers enhanced ESD protection on RS-485 I/O lines (Driver output / Receiver input) up to ±15KV. The SP485 part does not offer this enhanced ESD protection level. All other electrical parameters are the same between each part.
The following lines of code must be modified in the xr_usb_serial_hal.c file in the xr_usb_serial_set_flow_mode function at the end of the function:
Change from:
xr_usb_serial_set_reg(xr_usb_serial, xr_usb_serial->reg_map.uart_flow_addr, flow);
xr_usb_serial_set_reg(xr_usb_serial, xr_usb_serial->reg_map.uart_gpio_mode_addr, gpio_mode);
xr_usb_serial_set_reg(xr_usb_serial, xr_usb_serial->reg_map.uart_flow_addr, 0x0);
xr_usb_serial_set_reg(xr_usb_serial, xr_usb_serial->reg_map.uart_gpio_mode_addr, 0x3);
xr_usb_serial_set_reg(xr_usb_serial, xr_usb_serial->reg_map.uart_flow_addr, 0x0);
xr_usb_serial_set_reg(xr_usb_serial, xr_usb_serial->reg_map.uart_gpio_mode_addr, 0xB);
All of MaxLinear / Exar's USB UARTs are CDC class / CDC-ACM compliant, except for XR21B1421 which is an HID class device. This means they can use a native CDC driver. All major OS have native CDC drivers, except Windows prior to Windows 10.
None of the MaxLinear / Exar USB UARTs require their custom driver, however they will have certain limitations when not using it. The native CDC driver is not capable of accessing the internal memory map of any device. As a result, when using the native CDC driver, the device “defaults” to a particular configuration. The main implications of this default configuration are that hardware RTS/CTS flow control is enabled and that other settings / advance settings are not configurable. Some devices, for example the XR21B1411 which has an internal OTP memory, can be programmed to change this default configuration, but the configuration cannot be changed “on the fly”.
The COT families (XRP6141, XRP6124 and XR75100 controllers, XR76xxx regulators and XR79xxx power modules) have 2 modes of operation that can be set: DCM / CCM (discontinuous conduction mode / continuous conduction mode) or FCCM (Forced CCM) mode. In FCCM mode, the converter operates at a preset frequency regardless of output current. In DCM / CCM mode the converter operates in DCM or CCM depending on the Iout magnitude. If Iout < ½ Ipp, the converter transitions to DCM mode. If Iout is higher, operation is in CCM mode.
The main advantage of DCM / CCM is that it provides significantly higher efficiency at light loads. For those applications where that doesn’t matter, FCCM can be used and has the advantage that it allows for operation at a constant frequency, regardless of load. It also results in lower Vout ripple, and will operate in an inaudible range.
Size the inductor for 30% to 40% peak-to-peak inductor current ripple.
Size Cout for required load step transient response, for example <3% VOUT transient for a 0 – 50% rated current. Cout also needs to be sized for steady state output voltage ripple. Use effective value of capacitors corresponding to operating conditions.
Place small signal components close to their respective pins.
Place CIN capacitors close to PVIN / PGND pins.
Place inductor close to SW pin in order to reduce switching noise from this pin. Also keep the SW pin landing pad area as small as possible.
Size Cout for required load step transient response, for example <3% VOUT transient for a 0 – 50% rated current. Cout also needs to be sized for steady state output voltage ripple. Use effective value of capacitors corresponding to operating conditions.
Place small signal components close to their respective pins.
Place CIN capacitors close to PVIN / PGND pins.
There are many factors to consider in selecting the inductor including core material, inductance versus frequency, current handling capability, efficiency, size and EMI. Typically, the inductor is primarily chosen for value, saturation current and DC resistance (DCR). Increasing the inductor value will decrease output voltage ripple, but degrade transient response. Low inductor values provide the smallest size, but cause large ripple currents, poor efficiency and require more output capacitance to smooth out the larger ripple current. The inductor must be able to handle the peak current at the switching frequency without saturating, and the copper resistance in the winding should be kept as low as possible to minimize resistive power loss. A good compromise between size, loss and cost is to set the inductor ripple current to be within 20% to 40% of the maximum output current.
The switching frequency and the inductor operating point determine the inductor value as follows:
L = Vout x (Vinmax – Vout) / Vinmax x fs x Kr x Ioutmax
Where fs = switching frequency
Kr = ratio of the AC inductor ripple current to the maximum output current
So for example, we want to choose L for the XR76108 (Ioutmax 8A) and wish to convert 12Vin to 2.5Vout with a frequency of 1MHz:
In our example, Ipp = 35% x 8A = 2.8A
Once the required inductor value is selected, the proper selection of core material is based on peak inductor current and efficiency requirements. The core must be large enough not to saturate at the peak inductor current.
Ipeak = Ioutmax + Ipp/2
In our example, Ipeak = 8A + 2.8A/2 = 9.4A
In general, it is set for Imax x 1.5. It would be close the maximum Iout (including ripple). If conservatively set too high, the hiccup mode may not be activated fast enough. If set too low, the ripple could cause the current to go over the threshold and set it into hiccup on a pre-mature basis.
A zero-cross comparator monitors the voltage across the low-side FET when it is on. The comparator threshold is nominally set at -1mV or -2mV (see individual datasheet). If there is sufficient IOUT such that VSW is below the threshold and therefore does not trigger the zero-cross comparator, CCM operation continues.
As IOUT is reduced, VSW gets closer to ground. When VSW meets the threshold, the zero-cross comparator triggers. If there are 8 consecutive triggers, then DCM operation begins. The low side FET is turned off when IL x RDS equals the zero-cross threshold.
As there is no negative inductor current, the charge transferred to COUT is preserved. As IOUT decreases further, less charge transfer to COUT is required. Pulses grow further apart, frequency is reduced and efficiency increases.
DCM persists as long as there are 8 consecutive zero-crosses.
Note that when the DCM frequency falls below about 1kHz, the controller turns on the lower-side FET for 100ns once every 1.2ms to refresh the charge on the bootstrap capacitor. This refresh cycle generates small spikes on SW, which can be seen interlaced between DCM pulses.
For thermal and ESD benefits, the following PCB design is recommended to provide thermal and electrostatic paths:
1. Design the PCB to conduct heat away from the device using thermal vias under the QFN IC to the digital ground plane.
2. Mount the metal shells of the USB and Ethernet connectors to a separate Chassis / Earth ground.
3. Place the chassis / earth ground metal on one PCB layer, digital ground on another PCB layer and connect through a zero ohm resistor located away from sensitive electronic devices as much as possible.
4. Place a large metal trace for the Earth ground all the way surrounding the PCB, except under the Ethernet connector.
As an example, see the schematic and an example PCB layout for the XR22800 Evaluation Board below:




Please check that all the following conditions are satisfied first.
- no interrupts pending (ISR bit-0 = 1)
- modem inputs are not toggling (MSR bits 0-3 = 0)
- RX input pin is idling HIGH • divisor (the value in DLL register) is non-zero
- TX and RX FIFOs are empty
Be sure sleep mode bit has been set to 1. If there are multiple UART channels, the sleep conditions must be true for all channels.
See more on Sleep Mode in AN204 UART Sleep Mode.
Yes. Note: some devices do have powersave mode. If UART goes into powersave mode, then the registers are not accessible.
See more on Sleep Mode in AN204 UART Sleep Mode.
Read LSR register to check whether the UART receives the data or not.
- If LSR value is 0x60, it means that either UART receiver FIFO doesn’t receive the data or the data in receiver FIFO has been read out before the read of LSR.
- If LSR value is 0x00, it means data is still in the THR (clock doesn’t oscillate to transmit data).
- If LSR value is 0xFF, it means either UART is in powersave mode or UART is powered off. For those devices with powersave mode, be sure that UARTS are not in powersave mode.
See more on Sleep Mode in AN204 UART Sleep Mode.
- Check whether the register set can be accessed.
- Check whether the crystal is oscillating fully.
- Check whether the data can be transmitted in internal loopback mode.
See more on Sleep Mode in AN204 UART Sleep Mode.
