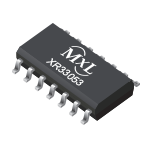
Overview
Information | ±60V Fault Tolerant 3.0V to 5.5V TIA-485/TIA-422 1Mbps Full Duplex Transceiver |
---|---|
Supported Protocols | RS-422, RS-485 |
Supply Voltage (Nom) (V) | 3.3, 5 |
No. of Tx | 1 |
No. of Rx | 1 |
Duplex | Full |
Data Rate (MAX) (Mbps) | 1 |
HBM ESD (kV) | 15 |
IEC 61000-4-2 Contact (±kV) | - |
Rx Fail-Safe | Advanced |
Multi-Drop Nodes | 320 |
Fault Tolerance (V) | -60 to 60 |
VL Pin | |
Temperature Range (°C) | -40 to 85, -40 to 105 |
Package | NSOIC-14 |
Transient Tolerance (V) | -100 to 100 |
ICC (Max) (mA) | 4 |
Shutdown | ✔ |
Typ Shutdown Current (µA) | 0.001 |
Hot Swap | ✔ |
PROFIBUS (5V) or High Output (3V) |
The XR33053 is a high performance TIA-485/TIA-422 transceiver designed for improved performance in noisy industrial environments and increased tolerance to system faults.
The analog bus pins can withstand direct shorts up to ±60V and are protected against ESD events up to ±15kV HBM. An extended ±25V common mode operating range allows for more reliable operation in noisy environments.
The receiver includes full fail-safe circuitry, guaranteeing a logic high receiver output when the receiver inputs are open, shorted or undriven. The XR33053 receiver input impedance is at least 120kΩ (1/10 unit load), allowing more than 320 devices on the bus.
The driver is protected by short circuit detection as well as thermal shutdown and maintains high impedance in shutdown or when powered off.
The DE and RE pins include hot swap circuitry to prevent false transitions on the bus during powerup or live insertion and can enter a 1nA low current shutdown mode for extreme power savings.
- 3.0V to 5.5V operation
- ±60V fault tolerance on analog bus pins
- Extended ±25V common mode operation
- Robust ESD protection:
- ±15kV HBM (bus pins)
- ±4kV HBM (all other pins)
- Enhanced receiver fail-safe protection for open, shorted or terminated-but-idle data lines
- Hot swap glitch protection on DE and RE pins
- 1µA (max) standby current
- Driver short circuit current limit and thermal shutdown for overload protection
- Reduced unit loads allows up to 320 devices on bus
- Industry standard 14-pin NSOIC package
- -40°C to 85°C ambient operating temperature range
- XR33052 – Half Duplex, 250kbps with hot swap protection
- XR33055 – Half Duplex, 1Mbps with hot swap protection
- XR33058 – Half Duplex, 20Mbps with hot swap protection
- XR33152 – Half Duplex, 250kbps with invert control
- XR33155 – Half Duplex, 1Mbps with invert control
- XR33156 – Full duplex, 20Mbps with VL pin, hot swap protection and invert control
- XR33158 – Half duplex, 20Mbps with invert control
- Industrial control networks
- HVAC networks
- Building and process automation
- Remote utility meter reading
- Energy monitoring and control
- Long or unterminated transmission lines
Documentation & Design Tools
Type | Title | Version | Date | File Size |
---|---|---|---|---|
Data Sheets | XR33052/3/5/8 ±60V Fault Tolerant 3.0V to 5.5V RS-485/RS-422 Transceivers | 2C | February 2018 | 787.7 KB |
Application Notes | Signaling Common Mode Voltage Operating Range Application Note | R00 | March 2025 | 2.3 MB |
Application Notes | RS-485 Transceivers in Fieldbus Networks | R00 | October 2024 | 2.4 MB |
Application Notes | AN-291, RS-485 Advanced Fail-Safe Feature | R01 | May 2023 | 3.7 MB |
Application Notes | RS-232 and RS-485 PCB Layout Application Note | R00 | December 2022 | 2.8 MB |
Application Notes | AN-292, RS-485 Cable Lengths vs Data Signaling Rate | R01 | July 2022 | 2.7 MB |
Application Notes | ANI-23, Fault Tolerant Testing | July 2017 | 574.3 KB | |
Product Flyers | ±60V Fault Tolerant RS-485 Transceivers | March 2019 | 742.8 KB | |
Whitepapers | How Robust Is Your Fault Tolerant Transceiver? | July 2017 | 129.3 KB | |
Product Brochures | Interface Brochure | R02 | November 2024 | 3.6 MB |
Quality & RoHS
Part Number | RoHS | Exempt | RoHS | Halogen Free | REACH | TSCA | MSL Rating / Peak Reflow | Package |
---|---|---|---|---|---|---|---|
XR33053ID-F | N | Y | Y | Y | Y | L2 / 260ᵒC | NSOIC14 |
XR33053IDTR-F | N | Y | Y | Y | Y | L2 / 260ᵒC | NSOIC14 |
XR33053HD-F | N | Y | Y | Y | Y | L2 / 260ᵒC | NSOIC14 |
XR33053HDTR-F | N | Y | Y | Y | Y | L2 / 260ᵒC | NSOIC14 |
Click on the links above to download the Certificate of Non-Use of Hazardous Substances.
Parts & Purchasing
Part Number | Pkg Code | Min Temp | Max Temp | Status | Buy Now | Order Samples |
---|---|---|---|---|---|---|
XR33053HD-F | NSOIC14 | -40 | 105 | Active | Order | |
XR33053HDTR-F | NSOIC14 | -40 | 105 | Active | Order | |
XR33053ID-F | NSOIC14 | -40 | 85 | Active | Order | |
XR33053IDTR-F | NSOIC14 | -40 | 85 | Active | Order | |
XR33053IDEVB | Board | Active |
Active - the part is released for sale, standard product.
EOL (End of Life) - the part is no longer being manufactured, there may or may not be inventory still in stock.
CF (Contact Factory) - the part is still active but customers should check with the factory for availability. Longer lead-times may apply.
PRE (Pre-introduction) - the part has not been introduced or the part number is an early version available for sample only.
OBS (Obsolete) - the part is no longer being manufactured and may not be ordered.
NRND (Not Recommended for New Designs) - the part is not recommended for new designs.
Packaging
Pkg Code | Details | Quantities | Dimensions |
---|---|---|---|
NSOIC14 |
|
|
|
Notifications
FAQs & Support
Search our list of FAQs for answers to common technical questions.
For material content, environmental, quality and reliability questions review the Quality tab or visit our Quality page.
For ordering information and general customer service visit our Contact Us page.
Submit a Technical Support Question As a New Question
For RS-232 it is 50 feet (15 meters), or the cable length equal to a capacitance of 2500 pF, at a maximum transmission rate of 19.2kbps. When we reduce the baud rate, it allows for longer cable length. For Example:
Baud Rate (bps) | Maximum RS-232 Cable Length (ft) |
19200 | 50 |
9600 | 500 |
4800 | 1000 |
2400 | 3000 |
Fail Safe is an attempt to keep the output of the RS-485 receiver to a known state. Transceivers may have standard fail safe or advanced / enhanced receiver fail safe features. Standard fail safe supports open inputs while enhanced fail safe transceivers such as the SP339 and XR34350 support open input, shorted input and undriven terminated lines without external biasing. See Application Note ANI-22 for more detail.
Find the product page of the part that you want to get an evaluation board for and click on Parts & Purchasing. Example:
Click on Parts & Purchasing or Order Now. Locate the icons under Buy Now or Order Samples:
Click on the Buy Now icon and see who has stock and click on the Buy button:
Alternatively, you can click on the Order Samples icon to request a sample.
Note, not all products are sampleable from the website.
If the icons are missing, create a support ticket.
Yes, this is possible using one RS-485 transceiver. The microcontrollers will have to be addressable and have tri-state outputs. The RS-485 device can be controlled by the host via the DE/RE pin. The micros will have to be in either receiving mode or tri-state mode when the RS-485 transceiver is transmitting data. When the host transmits it will have to send an address to the specific micro. If any micro transmits the transceiver will have to be in receiving mode and all other micros will have to be in receive or tri-state. So the host would have to initiate this sequence by addressing the micro first then switch the transceiver to receive.
The half duplex system would have a bus with one transceiver and multiple microcontrollers all tied to the bus. For 5V systems the SP485 family can be used. For 3V systems the SP3070 family can be used. The require speed will determine the part number. The SP3078 part runs up to speeds of 16Mbps. See the parametric search on https://www.exar.com/products/interface/serial-transceivers/rs485-422 for more options.
Care must be taken to assure the transceiver can drive the multiple micros in RX mode.
ESD tests are “destructive tests.” The part is tested until it suffers damage. Therefore parts cannot be 100% tested in production, instead a sample of parts are characterized during the product qualification. The test procedure consists of “zapping” pins with a given voltage using the appropriate model and then running the part through electrical tests to check for functionality or performance degradation.
ESD is caused by static electricity. In order for an ESD event to occur there must be a buildup of static charge. Very high charge levels are actually quite rare. In a normal factory environment, taking basic ESD precautions (grounding-straps, anti-static smocks, ionizers, humidity control, etc.) static levels can be kept below a few tens of volts. In an uncontrolled environment, like an office, static levels rarely get above 2000 volts. Under some worstcase conditions (wearing synthetic fabrics, rubbing against synthetic upholstered furniture, extremely low humidity)
levels can go as high as 12 to 15 thousand volts. Actually to get to 15000 volts or higher you would need to be in an uncomfortably dry environment (humidity below 10%) otherwise static charge will naturally dissipate through corona discharge. It would definitely be considered a “bad hair day.” Humans can generally feel a static shock only above 3000 volts. A discharge greater than 4000 volts can cause an audible “pop.” But repeated lower level discharges can be imperceptible and still may have a cumulative damaging effect on sensitive ICs. All ICs, even those with robust protection, can be damaged if they are hit hard enough or often enough.
Most ICs in a typical system are at greatest risk of ESD damage in the factory when the PCB is assembled and the system is being built. After the system is put together they are soldered onto the PCB and shielded within a metal or plastic system enclosure. Interface ICs are designed to attach to an external connector that could be exposed to ESD when a cable is plugged in or when a person or object touches the connector. These interface pins are most likely to see ESD exposure and therefore benefit from additional protection.
Actually the letter “E” could have two different meanings, depending on where it is in the part number. Most of our interface devices are available in different temperature grades. Commercial temperature (0 to 70C) has a “C” after the numeric part number. Industrial-extended temperature (-40 to +85C) use the letter E. So for example SP485CN is commercial and SP485EN is industrial. The second letter indicates the package type, in this case N for narrow-SOIC. Another E in the suffix indicates that this device has enhanced ESD protection, typically of ±15000Volts on the interface pins. Devices that do not have the enhanced ESD still contain built-in ESD protection of at least ±2000Volts. For example the SP485ECN is ESD rated up to ±15kV, and the SP485CN is rated for ±2kV HBM.
https://www.exar.com/quality-assurance-and-reliability/lead-free-program
Visit the product page for the part you are interested in. The part's status is listed in the Parts & Purchasing section. You can also view Product Lifecycle and Obsolescence Information including PDNs (Product Discontinuation Notifications).
To visit a product page, type the part into the search window on the top of the MaxLinear website.
In this example, we searched for XR33180. Visit the product page by clicking the part number or visit the orderable parts list by clicking "Orderable Parts".
The Parts & Purchasing section of the product page shows the Status of all orderable part numbers for that product. Click Show obsolete parts, to see all EOL or OBS products.
Videos
RS-485 Transceivers - Advance vs. Standard Failsafe
MaxLinear offers RS-485 transceivers with both standard and advanced receiver failsafe features. This video will show the main differences and advantages between advanced failsafe receivers and standard failsafe receivers in a typical RS485 installation.
Tips to Maintain a Successful RS-485 Link
This video provides four tips to help maintain RS-485 serial communication without data loss